新闻媒体
东莞市求精轴承有限公司(总部)
电 话:0769-22786416
0769- 23668162
传真:0769-22786419
手机:13669867858
邮箱:xgzhch@163.com
公司地址:广东省东莞市万江区牌楼基工业区 岳潭坊东一横巷5号
电 话:0769-22786416
0769- 23668162
传真:0769-22786419
手机:13669867858
邮箱:xgzhch@163.com
公司地址:广东省东莞市万江区牌楼基工业区 岳潭坊东一横巷5号
宁波市多辉轴承有限公司(分公司)
电 话:0574-86556187
电话:13713067019
传真:0769-22786419
网址:www.qjbearings.com
地址:浙江省宁波市镇海区贵驷街道贵安路24号
电 话:0574-86556187
电话:13713067019
传真:0769-22786419
网址:www.qjbearings.com
地址:浙江省宁波市镇海区贵驷街道贵安路24号

回转窑大瓦发热的征兆及预防
2020-05-22王占光
(焦作坚固水泥)
回转窑大瓦发热是比较闹心的事,有时几个瓦同时发热,有时几个瓦轮流发热,影响设备正常运行,给生产质量造成负面影响,如果能够通过观察某些征兆,判断瓦可能会发热,提前采取措施,就能减少被动,减少损失。(焦作坚固水泥)
一、在以下几种情况下,瓦有可能发热
1.窑皮垮落严重
在窑皮垮落严重时,回造成回转窑筒体半圈冷半圈热,受温差的影响,热的地方伸长的多,偏冷的地方伸长少,筒体就会弯曲,偏离回转中心的窑不但负荷波动,还会造成轮带产生扰动,轮带的扰动通过托轮传到瓦上,一旦扰动超出了球面瓦的自位能力,瓦与轴的接触将产生很大变化,局部超载不可避免,发热就会发生。
2.回转窑升温期间未能正常操作
若回转窑在升温期间,因各种原因未能正常操作,也容易正常筒体弯曲,同前一样容易正常大瓦发热。
3.临时停窑或故障停窑
临时或故障停窑,有时窑不能打慢转,也会造成筒体弯曲,引起轴瓦发热。
4.冷却水中断
冷却水中断后,瓦中的热量无法及时带出,势必造成油温升高,这样油的粘度就会下降,承载能力就会降低,一旦油膜遭到压溃、破坏,轴与瓦就会直接接触,摩擦力增加,引起发热。
5.润滑不良
润滑不良有多种形式,比如油量不足、布油不均、油变质、油污染等,这些不良情况的出现,都会造成润滑失效,一是运行产生的热量增加,二是带走热量的能力降低,若是油中有较硬的杂质,还会伤瓦,造成大瓦发热。
6.油膜发生变化
油膜发生变化,或变薄或变不均,或推力盘油膜发生变化,一旦发生变化,就说明瓦的受力已经变化,很可能造成发热。
7.环境发生了变化
环境变化会使瓦的散热条件发生变化,一旦破坏了平衡,瓦容易发热,比如环境温度因天气、筒体温度、通风条件等的影响,瓦温会升高,润滑油承载能力下降,一旦油膜遭到破坏或局部破坏,瓦就会发热。
8.异物进入
异物进入或灰尘或颗粒物料,会拉伤轴和瓦,造成接触精度下降或油膜破坏,会引起瓦发热。
9.调窑的影响
若窑筒体偏离了回转中心,就免不了调窑,但在调窑过程中改变了原来的受力状态,打破了平衡,就可能引起瓦的发热。
二、回转窑瓦发热的预防
回转窑瓦发热的原因很多,这就预示着预防的方法也多,可总结以下几个方面。
1.以风料煤及设备的稳定,调节好燃烧器,力保系统稳定,窑皮稳定,使窑筒体在正常回转中心运行,避免窑产生弯曲扰动。若真是出现了局部窑皮垮落,应通过调整,尽快将窑皮补上,补窑皮期间,应加强对瓦得监护,一旦出现油膜异常,可通过观察孔总轴上淋油或适当降窑速使瓦度过发热危险期。
2.无论是升温还是停窑,都要安规程操作,筒温高时连续慢转窑,温度低时间歇转窑;长期停窑期间,坚持定时对窑翻身,避免窑弯变形。一旦发现转窑过程中轴上油膜不均或局部油膜消失,就要采取措施进行筒体校正,比如连续慢转窑等,为了防止擦伤轴瓦可采取淋油措施等。
3.若出现如冷却水中断或其它冷却措施失效,应急时整改恢复,期间可通过淋油等措施冷却,避免长时间散热失衡,造成轴瓦发热。若环境条件发生变化较大,可采用风机加强冷却。
4.当润滑失效时,比如油位不足、油变质或污染、布油失效,应及时补、换相应牌号的润滑油,对油勺、布油板进行修正,期间可以适当降低窑速,补充其它冷却措施。
5、异物进入或块状或沙粒,会造成轴瓦拉伤,造成轴瓦发热,此时若发现是沙粒,应在观察孔加油并逐步放出,带出灰尘沙粒,若发现是块状异物或金属异物,若无法捡出,必须停窑捡出。
6、巡检中发现轴面、推力盘出现油膜发生变化,及时分析原因,比如窑弯曲、润滑不良、冷却水中断、进入异物等,并针对原因采取措施。
7.调窑很容易造成轴瓦发热,所以要小调整多观察,一旦油膜发生变化或较大,应采取紧急措施,比如暂停调窑或根据情况再少退一点或进一点,期间可以通过淋油加强冷却或尽快帮助恢复油膜。
回转窑的轴瓦发热之前,一般都原因,也有前兆,若能及时发现,及时措施,就会大大避免造成轴瓦的发热,影响生产,这就需要认真巡检,及时措施把控。以上只是笔者对轴瓦发热的预兆和预防的一些方法或看法,不对之处请读者批评指正。
(来源:智慧水泥)
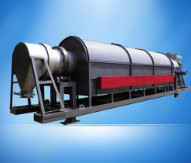